There are a lot of misunderstandings around about where corks come from and how cork products are made, so this article will aim to simplify the process to explain how natural cork and agglomerated cork products are made. Here you can see a diagram which shows the various processes and cork products that are produced. For the sake of simplicty we have shown just 3 product categories (expanded cork, natural corks and agglomerated cork products, shown in the yellow boxes).
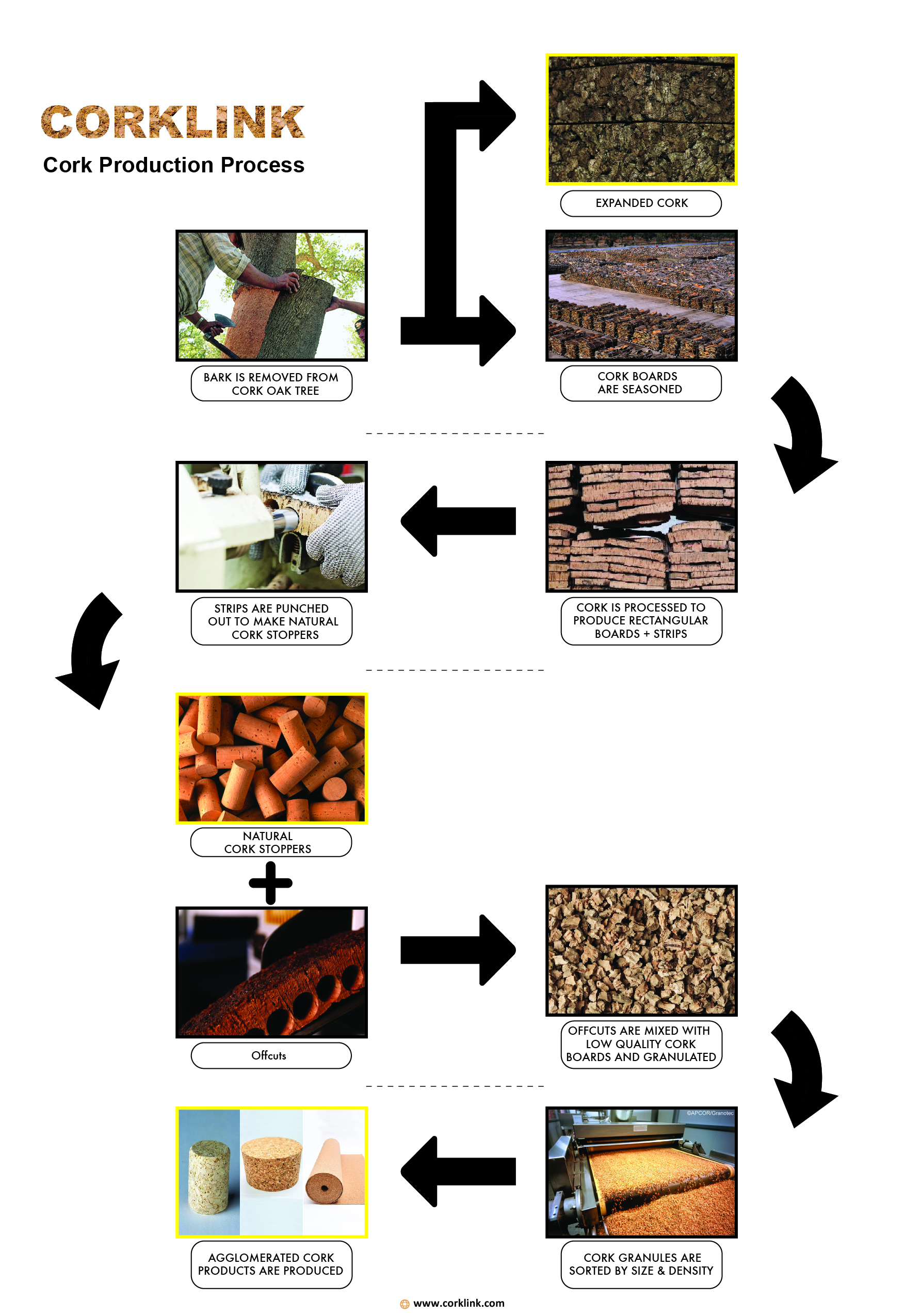
It all starts with the cork oak tree, which are abundant in Portugal but also found in lower numbers in various Mediterranean countries. The bark on these trees grows thick and spongey and every 9 years it can be removed to make cork. The tree does not die in this process and the bark just regenerates naturally and many cork oaks are over 100 hundred years old, having given up the bark multiple times to the cork industry. It is this fact that makes cork a fantastic renewable resource and CO2 sink, because the trees are never cut down. (The cork forests themselves are also support a unique and beautiful ecosystem, which you can read about on the link).
The cork bark has to be removed by specialist workers who work only in the Summer when the bark is more loose from the tree and use a very sharp axe to remove the cork in large boards, which retain the natural curvature of the tree. Most of these unprocessed boards are left to mature in the sun for up to a year, where they stiffen up ready to be processed to make natural corks and agglomerated cork products. The cork bark that is removed from the higher branches of the tree is more resinous and not suitable for standard cork production, so this cork bark is used to make expanded cork, where the resin is a vital part of the process.
The business of making the cork ready to be processed starts with boiling them, which softens the boards up to make them flat as well as sterilising the cork. These boards are then sorted for various qualities, with the best quality cork being used to make natural cork stoppers and the rest is passed through a crusher to make granulated (or used for decorative cork products).
The high quality cork boards are cut into strips with the thickness of a cork stopper and the natural wine corks are punched out of these strips. The off-cuts that are left over from this process are added to the crusher to make cork granules.
The cork granules are then sorted by sizes (generally from 0.2mm up to 12mm) and also by density – the outside edge of the bark is brittle and woody (with a high density) whilst the edge of the bark that is nearer the tree is much softer and elastic (low density). This means that the low density cork granules are much more valuable – there will be a range of densities available that have different end uses, from 60 kg/m3 right up to 250 kg/m3. These granules are then processed to make agglomerated cork products or in some cases such as cork infill for artificial turf, used in their granulated form.
So the story of cork is one of a completely sustainable product where every last bit is used productively and nothing gets wasted. The challenge to a cork supplier is to maximise the value out of every piece of the cork bark.