There are two methods for manufacturing agglomerated cork stoppers – individual moulds is a relatively new technology and is completely taking over from the traditional method of extrusion. The extrusion method is distinctly low-tech: cork granules are mixed with a binder in a hopper and forced through a cork diameter-sized hole to make a never-ending cork shaft. This shaft can then be cut into cork stopper lengths, which can then be processed with grinding stones to make smooth cork stoppers with a chamfer or whatever finish is required. The extruding machinery required to make them is relatively inexpensive, but has two major drawbacks: first the extruding process limits the density that the corks can be produced at and second it is not possible to have perfect control over the production process, mainly because gravity feed is not an exact process. This means that extruded corks are lower density and so weaker and there is more variability in the technical characteristics of one cork to another.
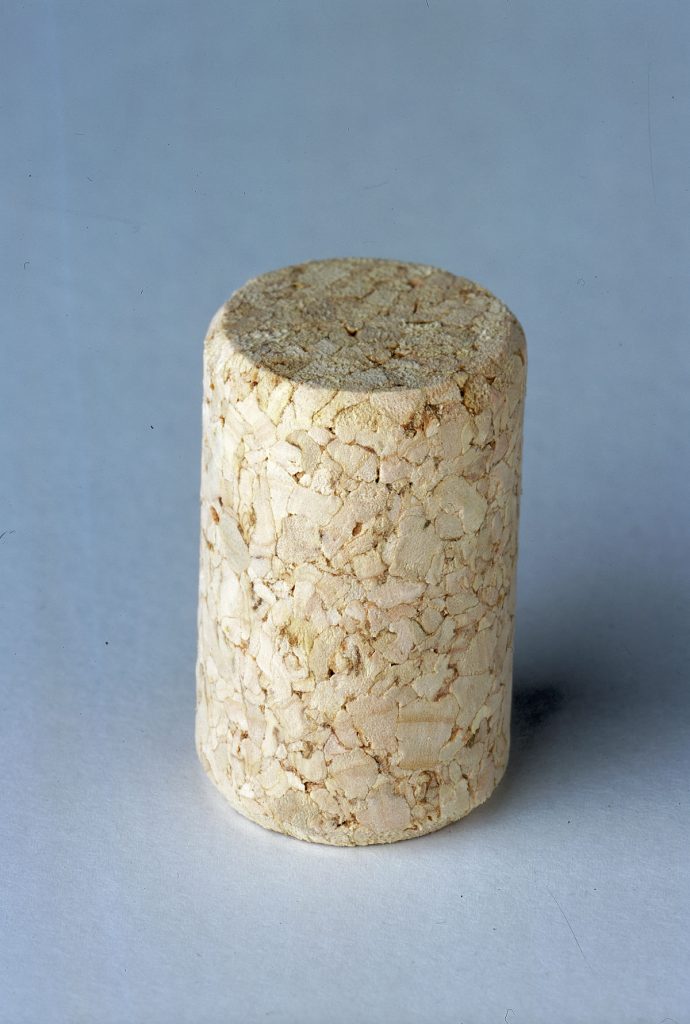
The individual moulding process is a lot more complex means of production, but provides stronger and more consistent cork stoppers. Moulded corks are always micro-agglomerated, which is to say that the granule size is between 0.5 and 2.0mm which helps to give the corks more structural consistency and precision in moulding. The small cork granules are fed into a compression moulding machine, which can cost over €1 million euros each and fully automate the production process. Just like with extrusion the granules are mixed with a binder, but then this is injected into cork shaped moulds, with the exact amount of granules being injected into each mould, where they are held under pressure. Still inside the moulding machine the corks are maintained at a high temperature where they are cured and once ready are expelled from the moulds.
The individual moulds of the corks can be made to any size and the dimensions and technical characteristics (including the density) can be controlled very precisely, so it means that the micro-agglomerated moulded corks have much greater structural stability than extruded corks and the technical characteristics are extremely tightly controlled so the consistency from one cork to another is also much greater. The cost of the moulding machines has fallen over time and they are also much more automated than extrusion machines, which helps to reduce labour costs, which has meant that the cost of moulded corks has fallen to nearer that of extruded corks, which explains why extruded corks are rapidly being squeezed out of the cork stopper market.

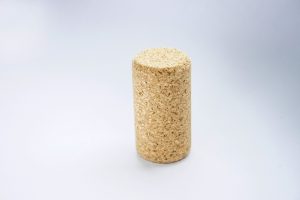
There are a few downsides to micro-agglomerated moulded corks compared to natural cork stoppers however – first the higher density makes the moulded corks very strong, but they are not as elastic as natural cork, so their fit in the bottle neck will not be so perfect; second the binder used is synthetic so the corks are not 100% natural, which is increasingly important for more environmentally aware consumers. Natural cork is of course 100% organic and biodegradable and its production is actually carbon negative, which can be a decisive consideration when considering the carbon footprint of the packaging. Finally, micro-agglomerated corks are very uniform, which can give them a slightly sterile appearance, whereas natural cork can have various markings and other imperfections, which like the natural grain in a piece of wood can add to their attraction. Of course the great benefits of micro-agglomerated corks is their consistency and the fact that they are generally much less expensive than natural cork (particularly good quality natural cork).
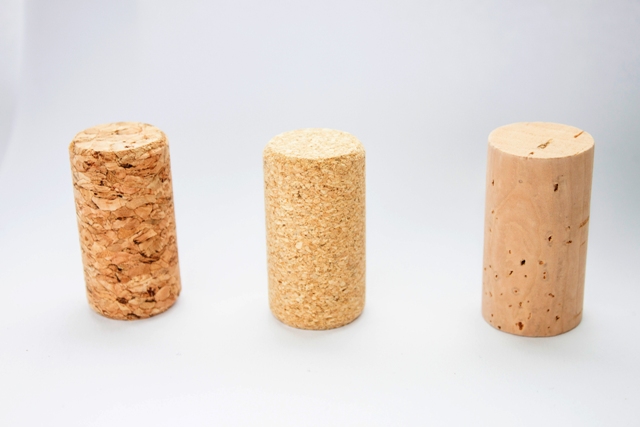
It seems inevitable that extruded cork will continue to lose market share to moulded corks, but the role of natural cork is harder to predict. We see a clear split among our cork stopper customers, with some looking for the low-cost reliability of micro-agglomerated moulded corks, but there are many who still prefer the more premium look and performance of natural cork (as well as the environmental benefits).