Most products that are to be made from cork such as cork lids, cork packaging and cork household items will either be made using a mould or via mechanical means. Many of our customers will initially think that a mould will be most appropriate, but in reality the vast majority of cork products that we produce are made using mechanical means. Here in this post we will look at the pros and cons of both methods.
First lets look at cork moulding – the standard way of doing this is to produce a two part mould from aluminium, the bottom cavity of which will be filled with a mixture of cork granules and a polyurethane binding agent. The top part of the mould is then placed on top and the entire mould goes into a hydraulic press for less than a minute. The mould can then be opened up and the cork products removed and left to cure in a temperature controlled environment. The products then have to be hand finished with sand paper to remove any excess granules left over and to tidy up the finish. Generally the maximum size is 300x300x200mm. The great advantage of this process is of course that all sorts of intricate shapes can be made using this process (although not with the same flexibility as injection moulding), but there are a number of disadvantages to consider. First the moulds themselves will typically cost €2500 or more and the prodcution costs are not that low, because the process is only partly mechanised and the moulding machinery is rather expensive also.
That takes us to the second option which is mechanical production – this involves several different options, including grinding stones, lathes, hydraulic press cutting/stamping, punching and numerous manual processes. With a reasonable amount of ingenuity it is in fact possible to make all sorts of interesting products using these more old-fashioned processes and there are a number of advantages to weigh against the main disadvantage that it is generally difficult to make intricate shapes (other than with cutting/stamping where tooling can be used to make cutting stamps for more complex designs). The key advantages are that there are virtually no set up costs, minimum quantities are typically 1000 units or less for larger items and the cost per piece are generally low. Furthermore, whilst moulding is restricted to having a particular blend of cork granule specification and binder, for machined items there are a range of specificaitions of agglomerated cork that can be used, including micro-agglomerated cork. Generally speaking the majority of cork products that are produced using these methods are circular because of the way grinding stones and lathes work (it is different of course for stamped items, but here the maximum thickness is 12mm).
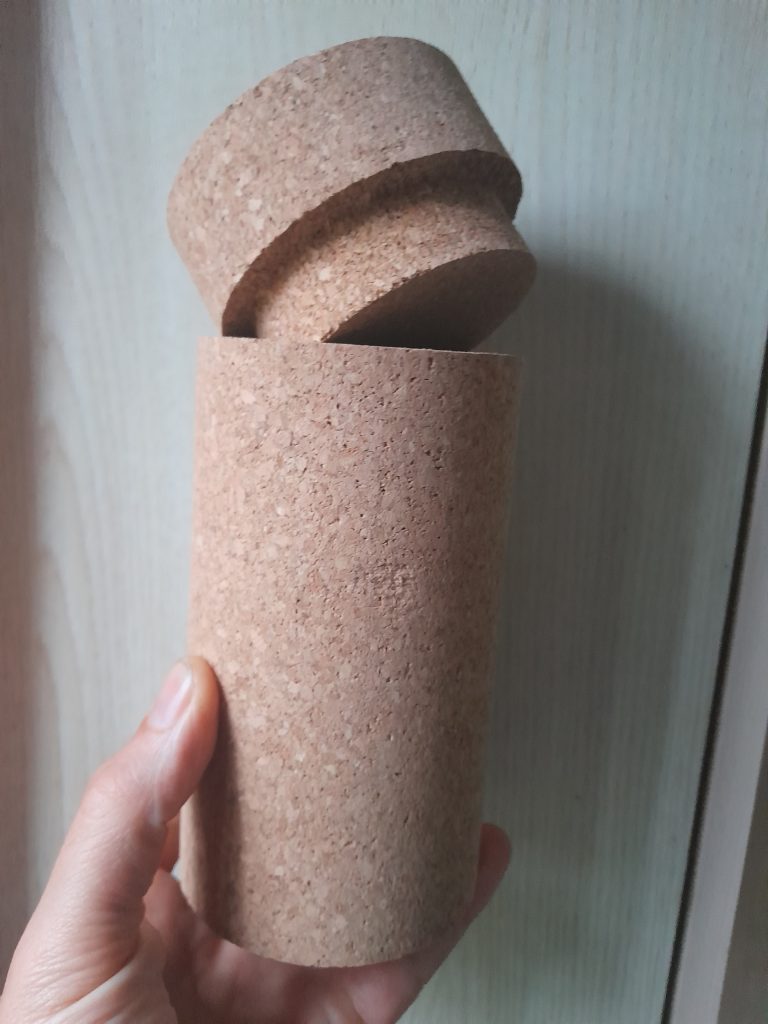
The final option for making cork products is using CNC, which can be a great option for complex shapes where moulding is not possible, but of course the cost per piece is much higher because the CNC machines are relatively slow and the machines themselves are so expensive.
The aim of this post is not to give a detailed explanation of how these different processes work, but rather to help our customers to understand that there are many different ways to make cork products other than moulding (and indeed that only a tiny proportion of cork products are actually made using moulds, other than cork stoppers). Very often they way things will work out is that customers will present us with a design and perhaps with only minor modifications we will be able to make the product using mechanical means to save them money and reduce the minimum quantities that will make the product viable. We have a lot of experience of making all sorts of fascinating products out of corks beyond our most popular products of cork lids and conical corks, so please send us over your designs so that we can best advise!