Both expanded cork and agglomerated cork are made from cork granules that are bonded together and here we will look at the key differences.
Agglomerated cork is made by grinding up of off-cuts of natural cork bark (generally resulting from the production of natural wine corks and natural bar-top corks) to form granules and then gluing the granules back together to form blocks (or compression moulded directly to form stoppers). Once the cork off-cuts have been ground up, the resulting granules need to be separated by density and size, because these two parameters will be key in determining their technical characteristics (you can read more about cork granule density here). As a result different kinds of agglomerated cork will require different densities of agglomerated cork, with the more prized low density granules generally being used to make micro-agglomerated compression moulded wine corks, medium density granules being used to make agglomerated cork for things like flooring and high density granules being used for example for infill. So the agglomerated cork that is made is a mixture of natural cork and a synthetic bonding agent (polyurethane), so once you make agglomerated cork, it ceases to be a 100% natural product.
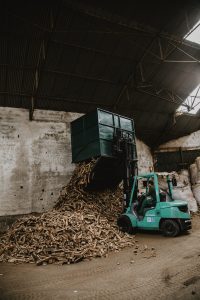
Expanded cork is made in a completely different way: in this case the source of the cork granules is directly from the tree bark and the bonding agent is the resin actually found within the cork granules themselves. The cork bark that is selected to make expanded cork is generally that considered to be too low quality to make natural cork stoppers with; so it will be bark from young cork oak trees or from the upper branches where there is not sufficient thickness of bark, but coincidentally there is much more resin. This cork bark is fed through a grinding machine to produce granules, but they are not sorted by density; instead they are fed into autoclaves, where pressure is applied as well as super heated steam. The autoclaves take around half a cubic meter of granules and the high temperatures cause the granules to swell up an release the resins they contain. Because they are in a confined spaces, these expanded granules are compressed together, but once the pressure is released, the natural resin binds the granules together to make a block. The key difference then with agglomerated cork is that the granules have expanded (so they contain more air making them better for insulation purposes) and the product is 100% natural. There are different densities of expanded cork that can be made according to how much pressure is applied in the production process.
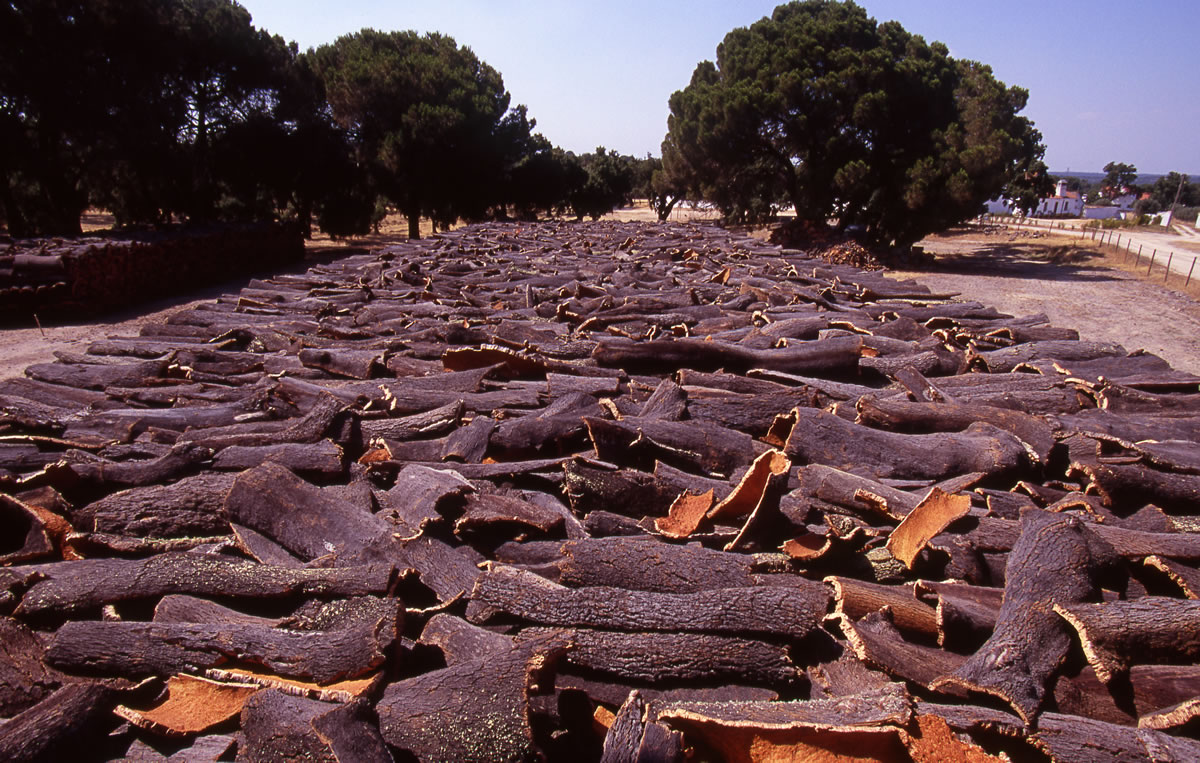
The visual appearance of agglomerated cork and expanded cork are completely different as the expanded cork is blackened by the heating process and of course the technical properties are of course completely different. The other key difference that is not so apparent is the fact that expanded cork is 100% natural and because cork oaks are not killed when their bark is removed to make cork (the regenerate their bark every 9 years), expanded cork is one of the few carbon negative insulation materials on the planet. If you are looking for agglomerated cork or expanded cork supplier, please contact us for more information.