Expanded cork is made in an autoclave, which is essentially a press where cork granules are added and placed under pressure and super-heated to make a block. The granules stick together because under the heat, the resin that is contained within the granules is released to form a natural kind of glue to bind all the granules together.
Under this process it is possible to adjust the amount of pressure that is applied to the granules, by squeezing them a little tighter so that the same volume of granules are squashed into a smaller space. When we do this, we produce higher densities of expanded cork. Our standard density expanded cork is made into a block of 1000x500x300mm (denisty = 115 kg/m3); with some extra pressure, we can make our high density block that comes out at size 1000x500x220mm (density = 155 kg/m3); and with maximum pressure we can make our very high density block in size 1000x500x120mm (density = 185 kg/m3). We can then cut these blocks into boards of thickness 10mm and upwards to make our final product.
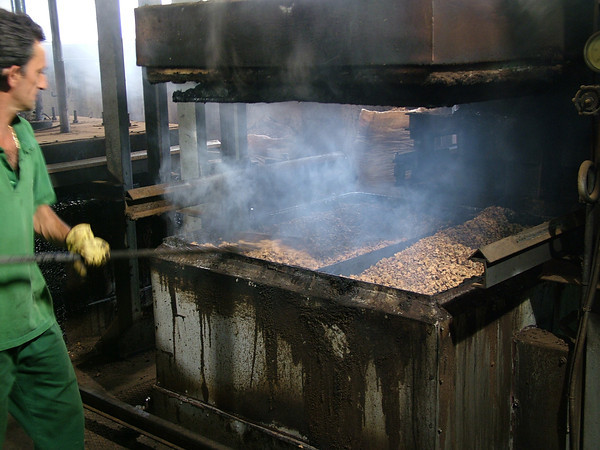
By adding density there is less air contained within the granules, so their insulation capacity is diminished a little. The main advantage of high density expanded cork is that it is a better acoustic insulation and vibration damper, but it is much less used than standard density expanded cork because it is around two thirds more expensive and it does not thermally insulate as well.
Generally we only advise that the very high density expanded cork boards are used when the expanded cork is going to be milled, as the higher density gives a more precise finish to designs. The high density version can be used when it is used for cladding that is likely to be constantly brushed against or otherwise impacted, because of its additional robustness. For decorative items and furniture for example, both high density and very high density can be used.
If you are looking for an expanded cork supplier or would like to know more about expanded cork densities, please contact us for more information.